IoT
デジタルツインとは? できることやメリット・デメリットを解説
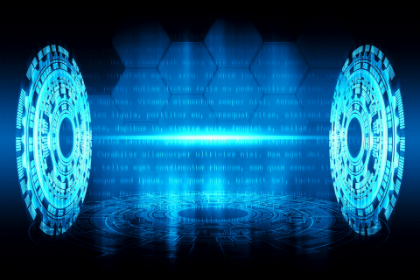
IoTやAI、5Gなどの普及とともに注目されるようになってきた「デジタルツイン」というワード。製造業の今後の進化を担うカギとなるテクノロジーと見なされ、他分野での展開も期待されています。デジタルツインとはどのような技術なのか、その概要をご紹介します。
デジタルツインとは
デジタルツインとは、フィジカル空間(現実世界)に存在する製品や製造設備の情報、およびそれらのオペレーションデータ、環境データなどをリアルタイムに収集しサイバー空間(仮想世界)に送って、サイバー空間上にフィジカル空間とまったく同じ状態・状況を再構築し、その仮想モデルを用いた高度なシミュレーションなどを行うという概念です。
あるいは、そのサイバー空間上に再現された、現実とそっくりな動的な仮想モデル自体をデジタルツインと呼ぶこともあります。日本語ではよく「デジタルの双子」と訳されます。
デジタルツインとシミュレーションの違い
デジタルツインはとくに製造業の生産現場に大きな変革をもたらす技術として期待されています。これまでの通常のシミュレーションと異なるのは、フィジカル空間とリンクしたデジタルツインを活用して、現実の製品には直接手を加えることなく、ほぼリアルタイムなシミュレーションを実施できる点です。
例えば、車のエンジンをさまざまなセンサーやカメラでモニタリングし、そのモニタリングデータを基にコンピューター上に本物と連動したエンジンの仮想モデルを作るとします。もしも限りなく本物と近い、「バーチャルな双子のエンジン」を作ることができれば、実在するエンジンに不調が発生したとき、仮想のエンジンを分析すればその原因を特定できるようになります。それだけではなく、本物のエンジンにこれから不調が起こりそうだという兆候も、仮想のエンジンを分析してわかる可能性があります。
また、この仕組みをもっと拡大して、工場の生産ラインや、工場全体の仮想モデル=デジタルツインを作ることも考えられています。デジタルツインを用いれば、サイバー空間でのシミュレーションによって、フィジカル空間に存在する生産現場でこれから起きる可能性の高い故障や変化の予測もできるようになるといわれています。
IoTやAIの技術とデジタルツイン
デジタルツインを作り出すにはフィジカル空間からサイバー空間へと送られる大量のデータが必須です。
そのデータを収集するための有効な手段はIoTです。製品や製造設備などが備えるセンサーやカメラが自動的にさまざまなデータを取得し、リアルタイムに送信し続けることで初めて、サイバー空間上にデジタルツインを構築することができます。
また、IoTが収集した膨大なデータを送信するには5Gの普及も大きなカギといえるでしょう。高速・大容量、多数同時接続、超低遅延・超高信頼性という5Gの特徴は、まさにデジタルツインが求める要件そのものでもあります。
そしてIoTと5Gによって送信され続ける膨大なデータを分析する役割を担うのがAIです。データを基に故障予測などのシミュレーションをする場合は、従来のシミュレーション技術に加えて、機械学習を主体としたAI技術を駆使して精度の高い予測をすることになります。
デジタルツインで実現できること
製品の製造工程で故障などのエラーが発生した場合、従来であれば作業員が時間と手間をかけて原因を特定するのが一般的でした。しかし、デジタルツインを導入すれば、サイバー空間上の仮想モデルを活用することで、どこでどんな問題が起きているのかの特定が、これまでよりも容易になると考えられます。またそれだけではなく、今後起こる確率の高い故障を予測することも可能になります。
故障予測は、ECサイトにおけるレコメンデーションと似た仕組みによって実現されます。レコメンデーションでは顧客の過去の購買履歴やページ閲覧履歴を記録し、それらのデータを分析して、顧客が最も興味を持ちそうな商品を推測してレコメンドします。
デジタルツインでは、これよりもはるかに複雑なプロセスと大量の仮想モデルを用いて精度の高い予測を行いますが、過去のデータから傾向を導き出し、現在のデータと突き合わせて推論し、ごく近い未来についての答えを見つけるという原理は変わりません。
フィジカル空間のデータを収集し、サイバー空間でシミュレーションして、その結果をフィジカル空間へフィードバックする、という手法は極めて汎用性の高いものですので、デジタルツインを製造業以外の分野で活用する動きも出ています。例えば、ビル、交通網、さらには都市そのもののデジタルツインを作るといった試みも進められています。
デジタルツインのメリット
デジタルツインを活用するメリットとしては、おもに次のような点が挙げられます。
- 製造設備の修理や部品交換などの保全を目的としたメンテナンス(予防保全)
- データを分析した結果を新製品の設計へとフィードバックすることによる品質向上
- 設計や製造のコストダウン
- 開発や生産に要する期間の短縮
- 適正な生産管理・在庫管理
工場などでの動きはデジタルツインに反映されるため、遠隔地からでも工場の状況を把握できます。故障や修理が必要な箇所なども即座に発見でき、メンテナンスを効率よく行えます。デジタルツインによるシミュレーションにより、予防保全も実現できるでしょう。
デジタルツインではさまざまな情報をデータとして扱えるようになり、分析も行いやすくなります。その結果を新製品の設計にフィードバックすることで、製品の品質向上も期待できるでしょう。デジタルツインは過去の情報をもとに、未来を予測するような使い方も可能です。
また、サイバー空間に工場などを作り上げることで、仮説検証や製品開発に関するシミュレーションも行えます。実際の工場の製造ラインを直接検証などに利用することはハードルが高いですし時間がかかりますが、サイバー空間上であればいつでも何回でも自由に組み替えて検証可能です。これにより、設計・製造のコストダウンや、開発・生産を効率的に行い、かかる期間を短縮することができます。
さらに、設計や製造に必要となるモノの管理の効率化も実現可能です。シミュレーションを通して製造まで行うことで、必要な部品・パーツを過不足なく把握できます。サイバー空間で検証・シミュレーションを行うことは、適正な生産管理・在庫管理の実現にもつながります。
デジタルツインは従来の業務を効率化・最適化し、生産性を向上させるだけでなく多くのメリットをもたらす概念です。製造分野だけでなく、あらゆる分野での活用が期待されています。
デジタルツイン活用におけるデメリット・課題
デジタルツインは多くのメリットをもたらしますが、課題も存在します。
デジタルツインはまだ発展途上の技術であり、代表的な課題の一つに「データの統合」があります。例えば、既存のデータをどのようにデジタル化するか、新しい技術を現実世界とどのように統合するのか、といった点が挙げられます。
その他には、デジタルツインを実現するにあたりコストが必要になる点や、技術者の確保が難しい点が挙げられるでしょう。加えて、特有のセキュリティリスクが発生する可能性があり、セキュリティ対策も欠かせません。さまざまな情報をデータ化してネットワーク上に流すことで、情報漏えいにつながる可能性があるため、不正アクセス対策や情報漏えい対策が必要になります。
コスト・セキュリティに関する課題も別途考慮する必要がある点は、デジタルツインを活用する際のデメリットといえます。
IoTやAIの普及とともに今後、デジタルツインの活用範囲も爆発的に拡がっていくことが予想されます。デジタルツインの導入について検討してみてはいかがでしょうか。