経営戦略
製造業が取り組むべき5Sとは? 活動の進め方やメリットなど
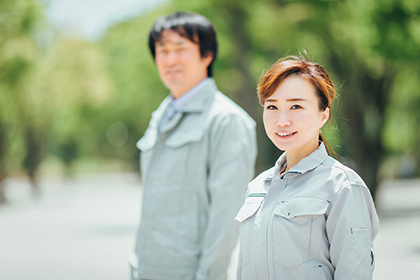
業務改善や職場の環境改善のための取り組みとして「5S」または「5S活動」というものがあります。とくに製造業は、この5Sへの取り組みが不可欠ともいわれています。5Sは何のために行い、どんなメリットがあるのか、その概要をお伝えします。
5Sとは
「5S」とは整理、整頓、清掃、清潔、しつけの5つの頭文字Sをとった言葉です。単に整理整頓や清掃をうながすだけではなく、職場環境を改善し維持するためのスローガンとしてよく使用されます。5つのSが意味する内容は次のとおりです。
整理
必要なものと不要なものを分別し、不要なものを処分することです。
整頓
必要なものをすぐに使えるよう配置や収納方法を工夫し、わかりやすく表示することです。
清掃
掃除をしてゴミや汚れのない状態を保つことです。同時に細部まで点検を行っていつでも使える状態にすることも意味します。
清潔
整理、整頓、清掃を継続して行い、清潔な状態を保つことです。
しつけ
これらをすべて実行できるよう指示し、習慣づけることです。
製造業が5Sに取り組む目的とメリット
5Sはもともと、昔から製造関連の企業が行っていた3S(整理・整頓・清掃)活動に、清潔としつけの2Sを加えて作られ、広まったといわれています。5Sはどんな業界・業種にも当てはめて実行できますが、中でも特に工場などの生産現場で重要なスローガンとなります。
製造現場で5Sに取り組む目的として挙げられるのは、作業環境の改善と、改善による安全性の確保です。作業環境がきちんと整理整頓され、掃除が行き届き、清潔さが保たれていれば、必要なときに必要なものをすぐに利用できるようになります。また、そのことによって現場の安全が保たれます。つまり、5Sは生産現場の最適化に役立つのです。
また、5Sへの取り組みにより、業務効率や生産性の向上というメリットが得られる可能性もあります。5Sが徹底されれば従業員のモチベーションアップにもつながります。5Sの内容はシンプルで、心がけ一つで誰もが実行できるため、製造現場で大きな効果を生み出すことが期待できます。
5S活動の進め方
5Sにはどのように取り組んでいけば良いのでしょうか。具体的な5S活動の進め方を見ていきましょう。
整理
5Sにおける整理は、必要なものと不要なものを選別することから始まります。問題は両者をどのようにして見分けるかです。この要・不要を見える化するための、よく知られている方法に「赤札作戦」があります。
赤札作戦ではまず、不要なものを見分けるための基準を作ります。基準は期限か、状態か、使用頻度か、重複したものがあるか、などで設定します。基準に合わないものには、そのものの処置期限や担当者名を書いた赤札を貼ります。そして赤札を貼ったものを一箇所にまとめて置き、処置期限が来るまで保管します。期間内にそのものを使わなかった、あるいは誰からも異議が出なかったら、ルールに従ってそのものを処分します。
このようにすれば不要なものを順次減らし、現場に必要なものだけを残していくことができます。
整頓
必要なものだけを残したら、次に整頓をします。整頓の基本は、定位置を決めて適正な数・量だけを置くことです。必要なものが常に同じ場所にあれば、使用するたびに迷わなくてすむので無駄が省けます。
新しいものが頻繁に追加される場合は仮置き場を作って対応します。また、同じようなものが多く見分けがつきづらいときはラベルや看板を使って表示するといった工夫も有効です。
清掃
清掃の目的は見た目をきれいにするだけではなく、安全で衛生的な状態を保つことにあります。製造業では機械や設備の点検・整備をしっかりと行き届かせ、異常や故障の予防に役立てることも含まれます。
清掃は「どのくらいきれいにするか」という基準を決めておくとやりやすくなります。理想的な状態の写真などを撮って共有しておくのも良いでしょう。その上で、いつ、誰が、どのような方法で清掃を行うかというルールを決めて実施します。
清潔
整理、整頓、清掃の3Sのプロセスを継続的に行っていくことで清潔な環境を維持します。
そのためには、所定の位置に置かれていないものや、清掃が行き届いていない場所などいつもと異なるものをおかしいと感じられるように、正常な状態を記録しておくことが有効です。写真などを用いても良いですし、チェックシートなどを利用しても良いでしょう。清潔さは生産性向上だけではなく、従業員の精神的・肉体的な健康を保つことにも結びつきます。
しつけ
ここまでのプロセスをルール化して周知し、組織的に実践できるようにします。しつけとは5Sの仕上げの段階といえます。研修の機会を設けるなどしてしっかりと情報共有し、全社的な意思統一をすることで、5Sが実効性のあるものになります。
この5S活動を実施すると、その中でうまくいくこともあれば、何かしら課題が出てくることもあるはずです。作業環境の改善、安全性の確保という目的を成し遂げるのは、それほどたやすいことではありません。さらに生産性向上などのメリットを得られるようにするには、試行錯誤を繰り返すことにもなるでしょう。
5S活動を行いながら課題を見つけ、対策を考えて、随時改善を行っていく必要があります。そうしたノウハウやナレッジを多く蓄積している企業ほど、生産性の高い、最適化された製造現場を作り出していくことができるでしょう。
5Sは単に職場をきれいにしようということではありません。とくに製造業においては、5Sを正しく導入し、システマティックに運用していくことが、組織力・企業力向上の大きな糧となるはずです。