経営戦略
生産管理のQCDとは? 強化のポイントも解説
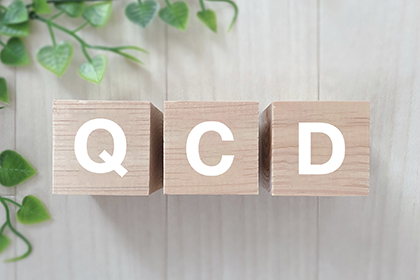
近年、製造業をはじめとして多くの企業は人手不足の課題を抱えており、業務の効率化や生産性の向上が求められています。その際に特に意識すべきものが生産管理のQCDです。このQCDについて、聞いたことはあっても内容まではよくわからないという方も多いのではないでしょうか。
そこで今回は、QCDについての基本知識から重要とされる理由、QCD強化に取り組む際のポイントについて詳しく解説します。
生産管理のQCDとは?
生産管理のQCDとは、「Quality:品質」・「Cost:コスト」・「Delivery:納期」の頭文字を取ったものです。生産管理における重要な3要素を示しています。
「品質」は業務全体の品質だけでなく、製品そのものの品質も表します。「コスト」は生産にかかる費用や時間のことであり、「納期」は製品を顧客に届けるまでの期限です。
品質・コスト・納期の3要素は互いに影響しあっており、一つの要素を優先すると他の要素が犠牲となるトレード・オフの関係にあります。
- Quality(品質):品質を高めれば顧客満足度が高まるが、コストの高騰・納期の遅れにつながる
- Cost(コスト):コストを削減すれば利益が得られるが、品質の低下・納期の遅れにつながる
- Delivery(納期):納期を短縮すれば顧客満足度が高まるが、品質の低下・コストの高騰につながる
あくまでも一例ですが、これらの逆もまたしかりです。普段当たり前のこととして取り組む生産プロセスのなかでも、QCDは深く関係しています。
それぞれの関係性を理解し、QCDを高めることは製品自体の価値向上だけでなく、生産プロセスの最適化にもつながり、業務の効率化や他社との差別化が期待できます。
QCDの優先順位と相関関係
QCDのなかで特に優先するべき項目は「Quality:品質」です。どれだけ低コストで最短納期が実現できたとしても、製品の品質が悪ければ顧客の満足度は低下してしまいます。あまりにも品質が悪いと信用を損なうことにもなるでしょう。
しかし、前述の通りQCDの3要素は互いに干渉し合うトレード・オフの関係にあるため、品質のみに注力してしまうと、コストの高騰や生産に時間がかかり納期が遅れる可能性があります。その場合も顧客満足度の低下につながります。
QCDの3要素のいずれかを優先してしまうとバランスが崩れてしまい、最大の効果を得ることはできません。それぞれの要素のバランスを考慮した上で、優先順位をつけて対応することが重要です。
一般的には品質を高めることを最優先とし、コストと納期は場合によって優先順位が変わります。予算や顧客の要望などの状況に合わせて、優先順位は柔軟に変更するようにしましょう。
QCDの強化に取り組む際のポイント
QCDを改善した上でさらに強化するためには、生産プロセスの効率化・改善が必須です。より効率的な生産プロセスを実現できれば、コストは低下し生産にかかる時間も短縮、最終的に品質も向上します。
生産プロセスの改善としてはじめに取り組むべきは、現場の意見を取り入れることです。現場レベルでの課題を抽出し、その課題に対して一つずつ改善策を立てて対策していきます。
改善策を実施する際には、QCDの優先順位を整理して数値として計測できる指標を作成することが重要です。例えば、顧客の満足度や作業ミス率などの指標を用いることで、生産プロセスの改善におけるQCDの強化が見えるようになります。
さらに、改善策は実施するだけでなく、その効果検証とより良い改善を継続的に行うことが必要です。しっかりと効果検証をしないと、そもそもQCD強化として成功しているのか失敗しているのかもわかりません。改善策を実施した際の成功・失敗の要因を特定し、次の改善策へ活かします。
このようなPDCAサイクル、「Plan:計画」・「Do:実行」・「Check:測定・評価」・「Action:対策・改善」を実施することで、継続的なQCD改善・強化につながります。
生産管理のQCDは相関関係にあり、1つの要素を優先すると他の要素が犠牲となる可能性があります。QCD改善のためには、このような相関関係を理解した上で、バランスが取れるように調整することが重要です。加えて、生産プロセスの改善によるQCD強化も実施しましょう。QCDの改善・強化は企業に多くのメリットをもたらすものですので、この機会にQCDについていま一度、意識してみてはいかがでしょうか。
日立ソリューションズ・クリエイトでは、工場のQCD強化を実現する「製造現場向けIoTソリューション」を提供しています。多様な製造現場に対して、IoTを活用してQCD強化を支援するソリューションです。